Tel: 0086-532-88966982
0086-532-88965892
Website: www.lidajituan.com
E-mail: sales@lidajituan.com
Head office: 5th Floor, Building A, Dalen Center, 180 Haier Road, Qingdao, 266000, China
Light Steel Structure Benefits Modern Factory Design Lida Group Construction Experts
Classification:Company News
Release time:2025-07-23 16:00
Light Steel Structure Benefits Modern Factory Design Lida Group Construction Experts
The rhythmic pulse of robotic assembly lines echoes through advanced manufacturing spaces where traditional construction methods struggle to meet precision demands. When a semiconductor manufacturer required vibration-free cleanrooms for nanoscale fabrication, conventional concrete structures transmitted disruptive harmonics from nearby utilities. Lida Group's engineered light steel structure solution delivered not just space but an environmentally stable platform where microscopic tolerances became achievable. This transformation represents manufacturing's quiet revolution – where buildings cease being passive containers and evolve into active precision instruments.
Modern factory operations confront multifaceted challenges that render obsolete construction approaches inadequate. Vibration-sensitive equipment demands near-absolute stillness impossible with conventional framing. Rapid process changes require layouts reconfigured quarterly without production shutdowns. Energy-intensive operations need thermally optimized envelopes reducing HVAC loads. Automation integration demands millimeter-perfect levelness for robotic navigation. Lida Group's expertise in steel structure building resolves these tensions through scientific material application and computational design.
The foundation lies in metallurgical innovation. Cold-formed S550MC high-strength steel achieves 45% greater yield strength than traditional materials, enabling slender structural profiles that maximize usable space. These alloys form the backbone of column-free production halls spanning 40+ meters – liberating factory floors from obstructive supports that constrain flexible manufacturing cells. The breakthrough emerges in how these materials are deployed. Computer-optimized truss geometries reduce steel tonnage by 28% while enhancing seismic resilience, creating structures that are paradoxically lighter yet stronger than conventional alternatives.
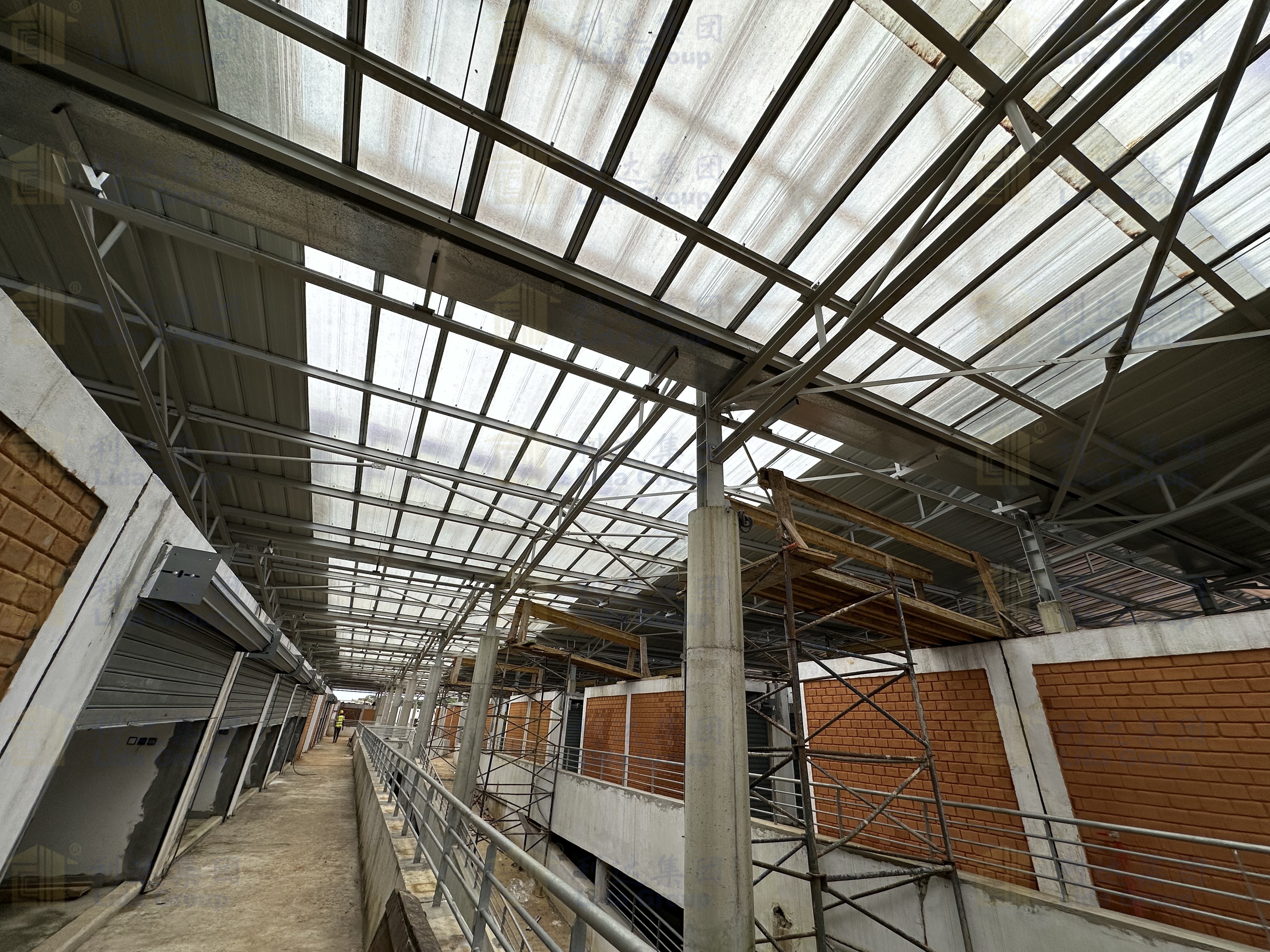
Material science extends beyond primary frames. Composite wall systems integrate aerogel insulation achieving R-38 values within slim profiles – critical for battery plants requiring strict humidity control. Nano-ceramic coatings applied in controlled factory environments provide ten-year corrosion protection in chemical processing zones. Phase-change materials embedded in floor slabs absorb excess machinery heat, reducing cooling loads by 35% during production peaks. Each selection serves dual purposes: structural integrity and operational enhancement.
Digital prototyping revolutionizes factory design before ground-breaking. Lida Group's virtual modeling simulates decades of environmental stress – predicting how Arctic temperatures affect weld integrity or desert UV degrades protective finishes. Computational fluid dynamics optimize airflow around heat-emitting equipment, while vibration analysis forecasts how structural harmonics impact calibration-sensitive instruments. This digital foresight prevents costly field modifications, ensuring facilities perform as engineered upon completion.
The manufacturing renaissance transforms specialized spaces. Precision workshop areas feature vibration-damped floors allowing micrometer-level metrology adjacent to forging presses. Quality control labs float on pneumatic isolators, creating stable environments where optical scanners detect sub-micron defects. Maintenance bays incorporate overhead crane systems rated for 80-ton transformers, with reinforcement precisely calculated for anticipated load paths. These aren't support spaces but performance-engineered assets enabling production excellence.
Warehouse integration achieves new synergies through structural intelligence. Automated storage systems require floor flatness tolerances under 3mm/10m – achieved through laser-guided pouring over optimized steel subframes. Clear heights extending beyond 28 meters accommodate vertical storage robotics, with roof structures engineered for future drone inventory systems. The distinction between production and storage dissolves as conveyor portals pass seamlessly through fire-rated walls, creating continuous material flows.
Energy infrastructure becomes architectural. Solar-ready roofs feature pre-engineered attachment points and concealed conduit pathways. Thermal banking systems store waste heat in salt hydrate-filled columns, releasing warmth during shift changes. Rainwater harvesting cisterns integrate into structural foundations, while wind baffles sculpted into parapet walls reduce HVAC loads by 19%. These features transform factories from energy consumers into regulated ecosystems.
For chemical plants handling volatile compounds, safety is engineered into connections. Explosion-resistant modular house control rooms feature blast-relief panels and positive-pressure ventilation. Flammable storage zones incorporate thermal break barriers and spark-resistant fixtures. Structural members near reaction vessels receive sacrificial cladding that signals corrosion before critical failure. Protection isn't added – it's designed from first principles.
The human dimension reshapes spatial planning. Ergonomic mezzanines position supervisors above production lines with optimized sightlines. Break areas feature circadian lighting combating fatigue, while acoustic baffles absorb 62dB of machinery noise. Escape stair towers incorporate wider treads and pressurized airlocks for emergency egress. These features reduce errors and turnover through environmental refinement.
Adaptability defines modern factory longevity. Bolt-together light steel structure infill walls reconfigure without cutting torches. Overhead utility grids enable tool-free power drop additions. Expansion joints in foundations anticipate future equipment weights. When an automotive electronics plant needed to upgrade cleanrooms, Lida's modular partitions reconfigured ISO classifications during weekend shutdowns – impossible with fixed construction.
Validation comes from extreme environments. At a copper processing plant in Chile's salt flats, galvanized steel frames withstand corrosive atmospheres that devoured conventional structures in three years. Arctic test facilities maintain ±0.3°C stability despite -45°C exterior temperatures. Coastal battery factories endure salt spray with specialized coatings showing less than 0.008mm annual corrosion loss. These facilities thrive where others fail.
Sustainability metrics reveal hidden advantages:
Future horizons push innovation further. Self-monitoring structures with embedded fiber optics detect micro-strains before cracks propagate. Phase-change windows dynamically modulate solar heat gain. Robotic construction platforms assemble complex nodes with 0.15mm accuracy. These advancements position light steel structure not as static infrastructure but as evolving platforms for manufacturing innovation.
Lida Group's legacy transforms factories from cost centers to competitive weapons. Their designs prove that when buildings actively regulate environments, dampen vibrations, enable reconfiguration, and integrate energy systems, they become precision instruments for production excellence. In this industrial paradigm shift, the most advanced machinery isn't on the factory floor – it is the factory itself.
light steel structure,warehouse,workshop,constructions,modular house
Contact Us
Head Office: 5th Floor,Building A,Darron Center,No.180,Haier Road,Qingdao, 266000,China
Tel: 0086-532-88966982 88965892 Fax:0086-532-88965571
WhatsApp:+86 13793209022
Mobile/Wechat:+86-15166671720
Email: sales@lidajituan.com Website: www.lidajituan.com
Alternate Website: www.lidamodularhouse.com
Head Office: 5th Floor,Building A,Darron Center,No.180,Haier
Road,Qingdao, 266000,China
Tel: 0086-532-88966982 88965892
Fax:0086-532-88965571
Email: sales@lidajituan.com
Website: www.lidajituan.com
Alternate Websit: www.prefabhousecn.com
Wechat/WhatsApp:+86-13793209022
Copyright(c)2023 All Rights Reserved SEO Business license